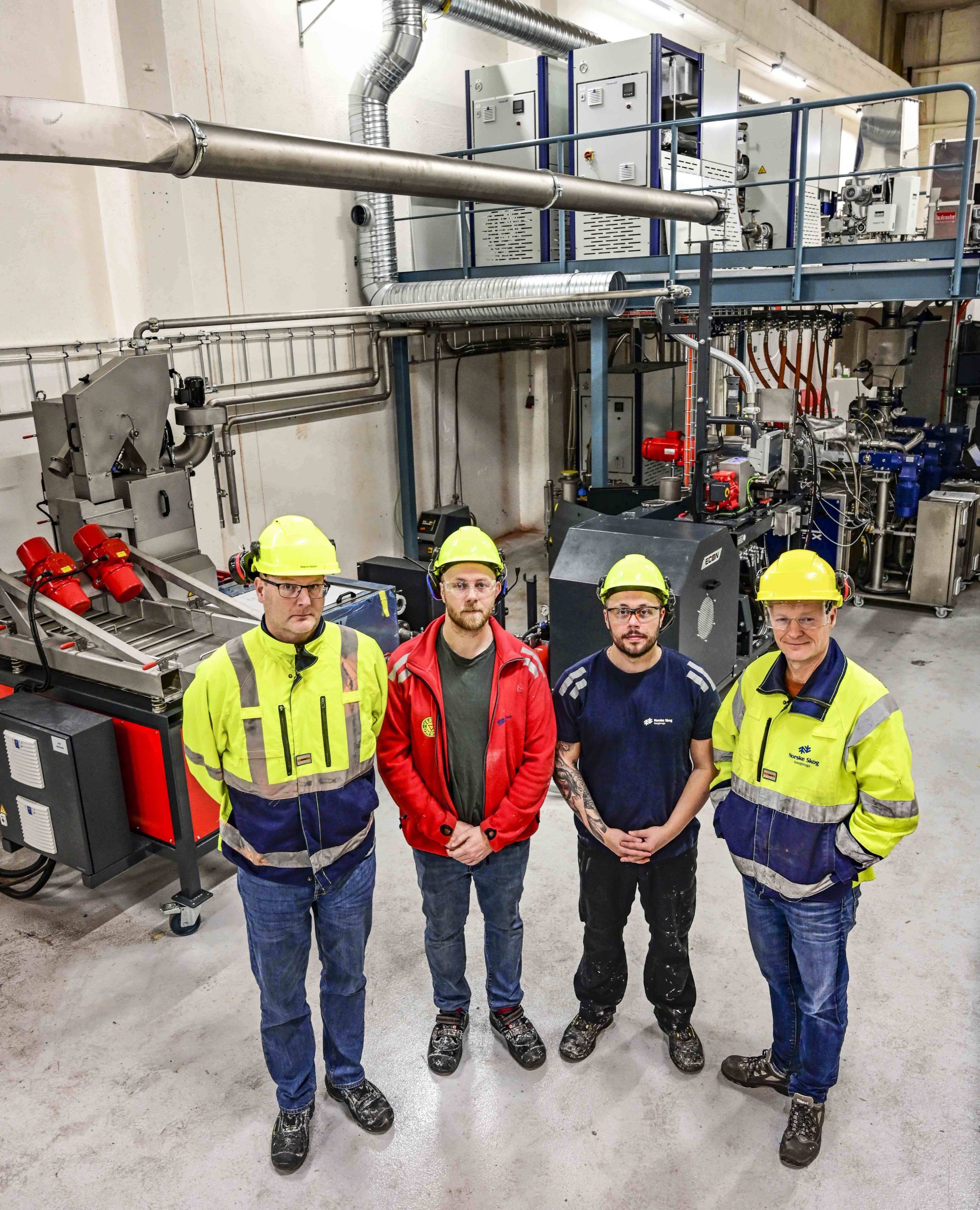
TESTER: Demoanlegget for Cebico som skal produsere testplast av tre på Saugbrugs er i gang. Magnus Sjøgren, Bjørn Einar Sundal, Aleksander Tsigras og Gudmund Jenssen skal være med å utvikle prosjektet gjennom erfaringer med det nye demoanlegget. Foto: Erik Sandersen, Norske Skog Saugbrugs.